Fuelling TheoryLet’s start with the theory then. We are concerned with spark ignition gasoline engines here. I’m only going to cover gasoline, since Diesel is for trucks and diggers, and alcohol is for drinking and drag racing.
ChemistryNow you might think that petrol is petrol right – not exactly. You will probably have heard the term ‘hydrocarbons’ before, perhaps as part of the MOT emissions check. Hydrocarbons are raw fuel – they are a chemical compound of hydrogen and carbon. Without getting into too much of the chemistry, there are different fuels, the simplest of which in structure (the alkanes) consist of chains of carbon molecules, each linked with the next carbon molecule and with two hydrogen molecules. The end carbons then have an extra hydrogen. This leads to a family of fuels with the chemical formulae CH
4, C
2H
6, C
3H
8 etc. These three examples are more commonly known as methane, ethane and propane.
Now because of the weird and wonderful way in which chemistry works, you can also get different arrangements of atoms, where the structures vary according to which H is bonded to what C, and how strong the bond is. Take for example C
7H
16. For the same number of C’s and H’s, it can be arranged in four different ways. Why is this important? Because the structure defines their properties as a fuel, and how they are broken down when they burn.
We’re all familiar with the RON value of petrol right? (If not don’t worry, I’ll come to it in a bit). A higher RON means the fuel is more resistant to knocking (self igniting). Well for our example C
7H
16, n-heptane has RON of 0, i-heptane (2,4-dimethylpentane) has a RON of 83, i-heptane (2,2-dimethylpentane) has a RON of 93 and good old i-heptane (2,2,3-trimethylbutane) has a RON of 112.
Overall a typical gasoline is predominantly a mixture of paraffins (alkanes), naphthenes (cycloalkanes), aromatics and olefins (alkenes). The exact ratios depend on the oil refinery that makes the gasoline, but with ever stricter requirements from manufacturers and government, gasolines from different companies are generally very similar in composition.
As you can imagine, there is a whole lot more to fuels than this, and that is why fuel companies spend a lot of money on research, playing with new blends of fuels and various additives (anyone remember lead) to improve certain desirable qualities. Here are a couple of interesting links to start you off.
http://www.atsdr.cdc.gov/toxprofiles/tp72-c3.pdfhttp://www.chevron.com/products/prodserv/fuels/bulletin/motorgas/3_refining-testing/If you need to know more about fuels, then find yourself a good book on the subject like I did. The information in this section ‘Chemistry’ is taken from Chapter 3 of ‘Introduction to Internal Combustion Engines’ by Richard Stone. Don’t act so surprised that I didn’t have all this info in my head. Hey I’m an engineer, not a chemist!
CombustionSo that’s the fuel itself, but how do we get any useful work out of it. Firstly we need to unite the fuel with oxygen (which comes in air as O
2). We mix the fuel and air together so that we get a good chance of O
2’s being near to C
xH
y’s, and if we have done a good job of mixing it (so that the fuel is spread out evenly through the air) the mixtures is called ‘homogeneous’, and this is the condition in which we will get the best combustion. Once we have ignited the mixture with a spark, a chemical reaction occurs where the C’s, H’s and O’s all swap around and end up as CO, CO
2 and H
2O, plus some extra heat. The heat makes these gases (combustion products) expand, and that drives the piston down the cylinder and voila – we have power!
Complete combustion occurs when just the right number of O
2’s are available to react exactly with the number of C
xH
y’s we have so that all the C’s H’s and O’s get converted. We express this ‘stoichiometric’ mixture as the ratio of mass of air (since we actually ingest air, not pure oxygen) to mass of fuel. This is the air fuel ratio – AFR, and this turns out to 14.7:1 for air:gasoline.
Another way to express the AFR is as the excess air factor – or to put it another way, the actual AFR/stoichimetric AFR. This value is called lambda. Lambda=1 equals AFR=14.7:1 for gasoline.
Lambda EfficiencyIn just the same way that the engine can still run with different spark advance, it can also run at different air fuel ratios. There are some pretty complex interactions occurring here.
As the fuelling increases, the incoming aircharge is cooled (as it loses its heat to the fuel), increasing the charge density, which as we know is a good thing.

The highest flame speed has been found by research to occur at a lambda of about 0.82. High flame speed is good because it increases thermal efficiency by reducing the time available for heat to be transferred to the cylinder walls, meaning the gasses expand more, and hence make more power.
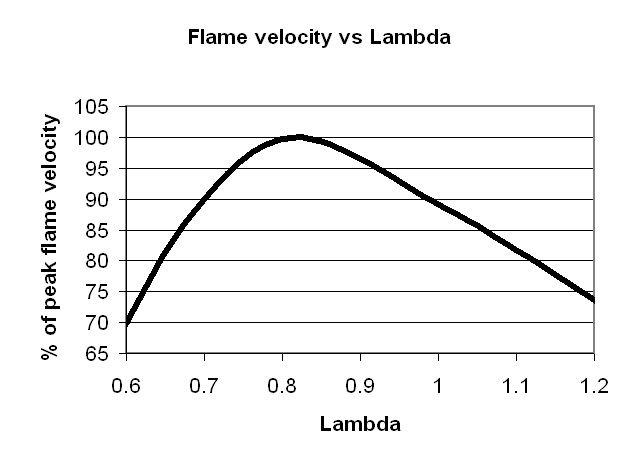
Theoretically, the highest combustion temperature occurs at the stoichiometric AFR, but in reality the highest temperature is reached at the lambda of around 0.88. This is due to thermal decomposition – and that’s about all I know about it. High combustion temperature is good because the more heat we get (assuming the engine can cope), the more expansion we get, and hence more power.
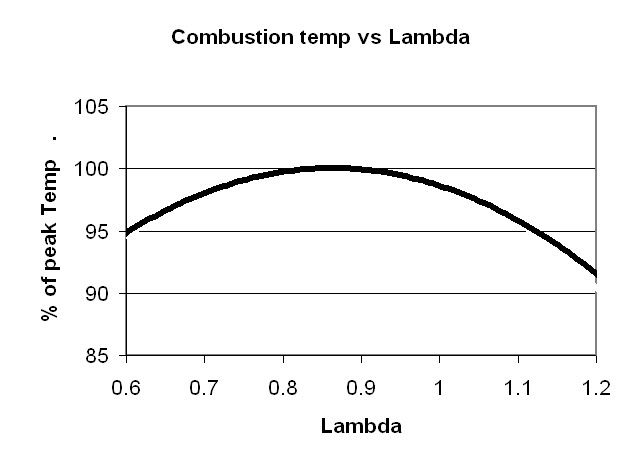
Lastly, the highest exhaust gas temperature is found at around lambda = 1.
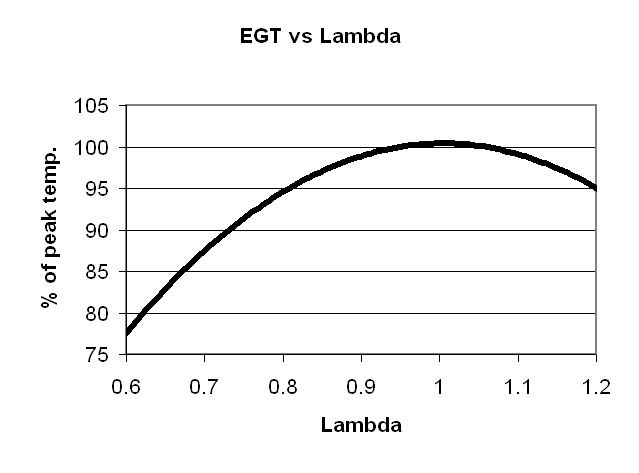
If we combine those effects, and if we consider the engine torque produced at stoichiometric to be 100%, then we can plot a lambda efficiency curve, just as we did with ignition timing.
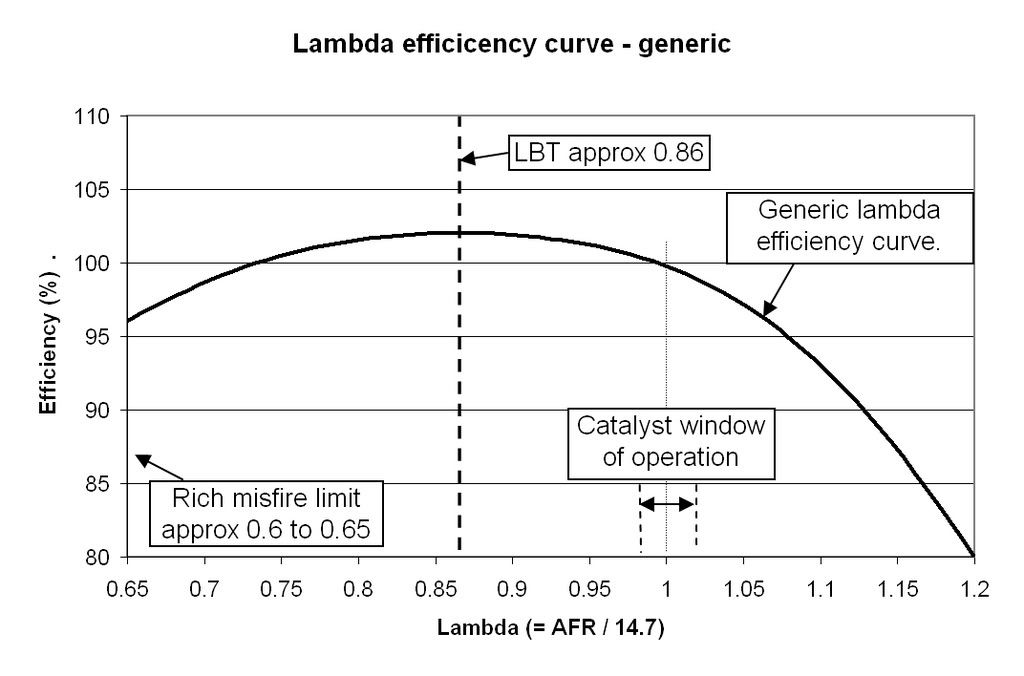
The key points are that the best lambda efficiency is at around 0.86, and this point is called the Lambda for Best Torque (or Leanest Best Torque, LBT). This is an important point to note.
ADDING MORE FUEL DOES NOT GIVE YOU MORE POWER. Lambda is simply a measure of the ratio of fuel and air in the cylinder. The only way to get more power from the engine (assuming you have optimised the ignition timing) is to burn more charge - the mixture of
FUEL AND AIR.The running limits of the engine are generally around lambda 1.2 on the lean side, and lambda 0.65 on the rich side. Outside of this region combustion becomes unstable, and eventually the engine starts to misfire as there is either too little or too much fuel for stable combustion.
Lastly, the catalyst window of operation is around 0.98 to 1.02, and the fuelling must be cycled between these two values in order for the catalyst to operate correctly. This will be important if you are fitting your engine management system to a vehicle that still has to comply with catalyst emissions limits for MOT or SVA. If you want to know why and how three-way catalysts work, have a look here;
http://en.wikipedia.org/wiki/Catalytic_converterFuel Octane NumberWe briefly touched on the RON value of fuel earlier, and I said I would explain a bit more – so here goes.
The octane rating of fuel is a measure of its knock resistance under fixed test conditions. For a description of knock, see the ignition section. The Octane Number scale is based around two known fuels – n-heptane, which was given an octane number of 0, and iso-octane, given an octane number of 100, for no other reason that these fuels were easily available in a pure form when this rating system was being developed. All other fuels are then tested using a single cylinder research engine of variable compression ratio, and compared against these two reference fuels. From these tests, the fuels octane number is derived. Note that these 2 fuels do not represent the ends of the scale – ironically n-octane has a RON of -20, and methane has RON of 120. Additives can increase this even further – US wartime aviation gasoline was commonly as high as 150 RON. Unfortunately many of these additives are either incompatible with catalysts, bad for the environment, expensive- or all three! This generally makes very high octane ‘race’ fuel a rare and expensive breed.
There are several different ways of quoting the octane number. In Europe, we commonly use the Research Octane Number (RON). However, another (and some may say more representative method) is the Motor Octane Number (MON), which provides a value under different test conditions to RON, but still using the same reference fuels. In the US, the quoted value is sometimes the roaD Octane Number (DON), also called the Anti Knock Index (AKI), which is the average of the MON and RON values of the fuels. This used to be an important distinction, since fuels of the same RON may have different MON values depending on the blend of the main constituents. Nowadays however, with increasingly stringent legislation and requirements on fuel blends for cars, the RON can generally be considered as being 10 points greater than the MON of available pump fuel, and hence the DON and AKI is halfway in between.
Here is another important point to note.
RUNNING ON A HIGHER OCTANE FUEL DOES NOT GIVE YOU MORE POWER. The extra power comes from advancing the ignition timing to take advantage of the better anti knock properties. Modern OEM systems do this for you (active knock control) and most high performance engines with cylinder individual knock control are now calibrated on 100RON fuel, and the knock control system adjusts the ignition timing to allow them to run sfely on 98, 95 or even lower RON fuels. However, aftermarket systems (that I know of) still do not have this fine a level of control, and any ‘knock control’ functionality is a safeguard at best. Therefore, as I said in the Ignition section, map the car on the fuel you intend to run. If you think you might want to run different types of fuel, then you will need to map the car on each type. As we will see, this is not just ignition mapping, but affects the target lambda maps too.
VolatilityAs well as all the other requirements we put on fuel, it also has to cope with changing temperatures and barometric pressures. Remember I mentioned mixing the fuel with air? Well one part of this mixing is through evaporation, or vaporisation. As we already know, gasoline is actually composed of a complex mix of fuels. Some of these will turn into vapours (gasses) at quite low temperatures. Others will remain liquid until they get quite warm. During starting the engine, the amount of airflow and hence fuel required is relatively small. This means that the physical mixing of fuel and air is less effective, since there is less charge motion to help break up the droplets of fuel and mix them with the incoming air. This is where we rely on the ‘light ends’ of the fuel to vaporise. It is this part of the fuel that starts the car – much of the rest of the fuel is wasted initially until the combustion chamber and inlet ports warm up, and we are able to increase the engine airflow. This is why we increase fuelling for cold temperatures, but we’ll cover this in more detail in the starting section.
So when the weather is cold, we need a high volatility fuel that vaporises easily to allow easy starting. The flip side of this is that when everything gets too hot, liquid fuel can turn to vapour in the fuel rail and cause a ‘vapour lock’, whereby when you open the injector you get nowhere near the amount of fuel you expect (the density has decreased dramatically). This commonly occurs after the car has been driving until warm and then stopped for 20 – 40 minutes, allowing the heat of the engine to ‘soak’ into the engine components and the fuel in the rail itself. To avoid this we need a low volatility fuel. We can also increase the starting fuel, just as we do when cold, to compensate for the reduced density effects.
To try and meet these 2 conflicting requirements fuel companies actually change the volatility of the fuel available during the year. In some countries this may be in 2 or 3 steps through the year. In the UK we normally just have winter (high volatility) and summer (low volatility) fuels.
As an aside, you’ve heard people say they left the car for a while and when they came back the petrol was ‘stale’. All that means is that the light ends have vaporised from the fuel in the tank, and left only the low volatility fuel. In extreme cases this will make starting the car difficult, but in reality there is nothing much wrong with the fuel. Mixing it 50:50 with some fresh (preferably winter) fuel will normally solve the problem (if there is one) and mean you don’t have to throw it away.
Fuel DensityFuel does in fact change in density with temperature, significantly enough to warrant attention. The chart shows the curve that was generated for the fuel dispensing industry in order to correct the delivery of fuel pumps.
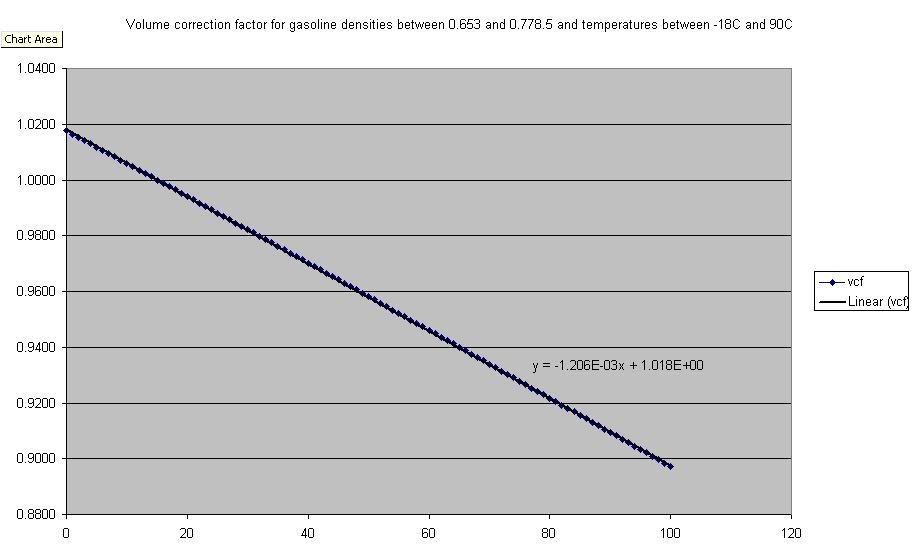
In the engine, our air fuel ratio requirement is based on mass. But injectors are flow devices. So in order to calculate the correct mass of fuel from the injector open time, we also need to know the fuel density. Or to put it another way, in order to inject the correct amount of fuel under all conditions, we need to correct the injector pulse width based on the fuel temperature, using the percentage corrections above.
Over-fuelling – why do it?You’ll have seen tuned cars (usually turbocharged) at the track which when accelerating hard leave a trail of black smoke behind them. This is one side effect of serious over-fuelling. We can see from the theory above that we would ideally run around lambda 0.86 for peak lambda efficiency, but there are 2 good reasons for running richer than this.
Due to the high gas flow rate at high engine speeds, and under heavy loads, the exhaust components (e.g. exhaust manifold, turbo, O
2 sensors) are subjected to very high temperatures. In order to keep these components at or below their temperature limits (800 to 950°C), the fuelling is increased (richened) to lower the exhaust temperatures. This happens because of the lower combustion temperature of mixtures richer than lambda 0.88, and the initial charge cooling effect of the additional fuel, as we have seen.
The very same cooling effects also reduce the chance of knock during combustion, since the in cylinder charge and combustion temperatures are lower. This is why some tuners take the approach of running extremely (some may say excessively) rich mixtures, in order to allow more spark advance, and to protect the engine components from excessive temperatures.
Personally that’s not how I calibrate engines (who wants their car to look like a diesel when they tip in?), as I feel it’s wasteful of fuel for a minimal benefit. It also increases the chances of other problems - more delivered fuel requires larger injectors, more pump capacity etc, and the excess fuel may increase bore washing effects (where the fuel literally washes the lubricating oil film from the cylinder walls), reducing piston ring and cylinder life. However, I can understand the rationale and the potential for a little more power, so if that’s the only thing that matters to you, then feel free to try it.